Light on – pick – confirm – light off.This used to be the extent of the function of pick by light systems – and in the minds of many users it`s still the case today. However, modern pick-by-light systems not only effectively support the order picker, but also the operator, the maintenance technician, the controller and the person responsible for quality management in optimising processes.
This concerns, for example, the following questions: How often is the picking quantity corrected by the picker? Which shelf display is used the most? Which telegram errors have occurred, how often and why?
Each question concerns a different area of responsibility, such as the warehouse management system, maintenance or network technology.
Modern pick-by-light systems support up-to-date diagnosis for fast problem solving and help to identify optimization and cost saving potentials by numerous functions for recording and analyzing process data.
KBS Industrieelektronik GmbH, one of the leading European suppliers of pick-by-light systems, presents some of these assistants:
“Picking Monitoring & Alert”
Collection and analysis of all relevant order picking processes in the pick-by-light system with dashboard preparation and a messaging function
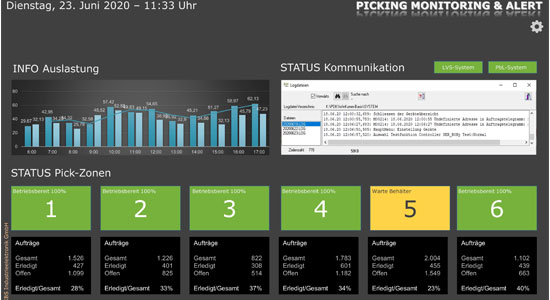
Dashboard Picking Monitoring
This assistant provides information in graphically prepared form about all processes directly connected with the order picking, such as pick orders per day, week or month, pick orders completed and still open in total or per pick zone, utilisation rate per pick zone or pickinig performance per pick zone etc. A messaging function can be activated when freely definable limits are reached (up or down).
“System Monitoring & Alert”
Collection and analysis of internal system messages with dashboard preparation and messaging function
This assistant provides information in graphically prepared form about all processes and events that occur within the pick-by-light system, such as the total number of times each individual button of each shelf display is pressed, their operating temperature and voltage, the current consumption of the interface units, possible error messages of shelf displays (e.g. eye-catching lamp defective), failures of system components, possible error messages of the bus system (e.g. short circuit), possible telegram errors, and much more. A messaging function can be activated when critical errors occur or when freely definable limit values are reached (up or down).
“Process Data Documentation”
This assistant takes on, stores and archives process data via a log server function in any desired location – local, central or in a cloud and thus enables secure long-time archiving for meaningful and verifiable process documentation.
“Intelligent Replenishment”
This assistant integrates a replenishment request function directly on the shelf display, either manually by the picker or fully automatically by means of a sensor in the rack. Process reliability and performance are increased, waiting times or cancelled orders are minimized.
“Call for assistance”
In case the picker gets stuck: This assistant integrates a call function to the team leader via SMS, e-mail or voice message directly from the shelf display
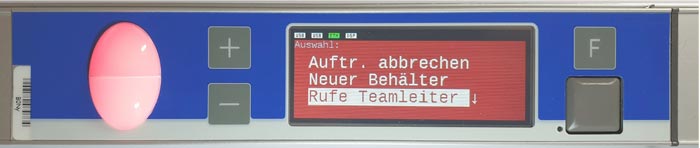
“Call team leader” function directly from the zone display
In most cases, these assistants can also be retrofitted to existing pick-by-light systems from KBS.